Corrosion-Resistant stainless steel 304 & 316 gas spring
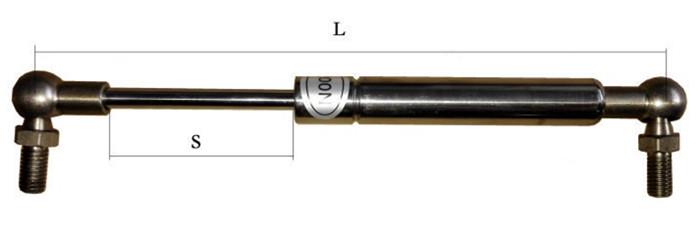
Features & Benefits
304/316 Stainless Steel Tube and Rod End of Travel Dampening
Designed & built to the highest gas spring manufacturing standards
High life cycle design
Low electrolytic capacity
Corrosion Resistance
Low magnetic signature
Multiple end fitting choices
Ideal for marine, petrochemical, pharmaceutical, medical, and food industry applications,and high technology industries
applications for stainless steel springs
Marine applications
Food service and processing equipment
Petrochemical
Medical and Pharmaceutical
Applications requiring non-magnetic components
Steel or stainless steel gas spring: which is better?
Is a steel or stainless steel gas spring better? Basically there is no “wrong” or “right” in this case. Both materials have certain properties that show up better in different circumstances. For example, a steel gas spring is less practical if the application could possibly come into contact with water or moisture in any way. The gas spring will eventually rust, show traces of corrosion and break. Something you would of course want to avoid.
Difference between stainless steel 304 and stainless steel 316
The big difference between stainless steel 304 and stainless steel 316 is in the composition of the materials. Stainless steel 316 contains 2% molybdenum, which makes the material more resistant to crevice, pitting and stress corrosion cracking. The molybdenum in stainless steel 316 makes it less sensitive to chlorides. This property in combination with a higher percentage of nickel increases the corrosion resistance of stainless steel 316.
The weak point of stainless steel 304 is its sensitivity to chlorides and acids, which can cause corrosion (local or otherwise). Despite this drawback, a gas spring made of stainless steel 304 is an excellent solution for home-garden-and-kitchen applications.
A gas spring made of stainless steel 316 is the solution for aggressive environments where chlorides and acids are used. Due to a different composition, this material is more resistant to corrosion and environmental influences, such as at the coast or in salt water. In addition, gas springs made of stainless steel 316 are of higher quality. These gas springs have a grease chamber and a built-in clean cap. A grease chamber ensures that the seal of the gas springs is always well lubricated, so that it does not matter how the gas springs are positioned. These gas springs can therefore also be mounted with the piston rod upwards or be positioned completely horizontally, without the seal drying out and the gas springs starting to leak. A clean cap ensures that the piston rod is scraped clean, so that no dirt gets into the interior of the gas springs. As a result, the stainless steel 316 gas springs can also be used in dirty environments. So very multifunctional!
Choose the right alloy
Think carefully about the choice of a certain alloy. This largely determines the success of the application. A mismatched alloy can sooner or later cause rust or reduce its lifespan. Of course you can always go for the highest possible quality, such as a gas spring made of stainless steel 316, but then you are also a lot more expensive in costs and you may pay for features that you do not need. When choosing, consider the environment, the surface finish and the budget.